Welding inspection services are a fundamental requirement for industries that rely on welded structures, ensuring that every joint meets strict safety and quality standards. These inspections verify the integrity of welds, identifying defects that could compromise structural performance or lead to costly failures. From pipelines to industrial machinery, businesses depend on precise inspection methods to confirm compliance with international regulations and maintain operational efficiency. Without professional welding inspection, undetected flaws can result in equipment breakdowns, production delays, or severe safety risks. That’s why industries invest in expert Welding inspection services to safeguard their assets, minimize downtime, and enhance the longevity of their welded components.
What Are Welding Inspection Services?
Welding inspection services ensure that welded joints meet industry standards for strength, durability, and safety. These services involve thorough evaluations using advanced testing techniques to detect defects, inconsistencies, or weaknesses that could compromise structural integrity. By adhering to strict regulations, welding inspection guarantees the quality of welded components, reducing the risk of failures and costly repairs.
The Role of Welding Inspection in Structural Integrity and Safety
In industries where welded structures must endure extreme pressures, temperatures, and environmental conditions, even the smallest flaw can have serious consequences. Welding inspection services help prevent such risks by ensuring that welds are free from cracks, porosity, or incomplete fusion. Proper inspection enhances the reliability of equipment, prevents structural failures, and ensures compliance with international welding codes. This not only protects assets but also safeguards workers and surrounding environments from potential hazards.
Industries That Rely on Welding Inspection Services
A wide range of industries depend on welding inspection and quality control to maintain the integrity of their welded components. These include:
- Oil & Gas: Ensuring the safety of pipelines, offshore platforms, and refineries.
- Construction: Verifying the strength of bridges, buildings, and steel frameworks.
- Manufacturing: Maintaining quality in aerospace, automotive, and heavy machinery production.
- Power Generation: Inspecting welded components in energy plants and pressure vessels.
- Petrochemical: Preventing leaks and failures in chemical processing plants and storage tanks.
How Welding Inspection Services Improve Quality and Compliance
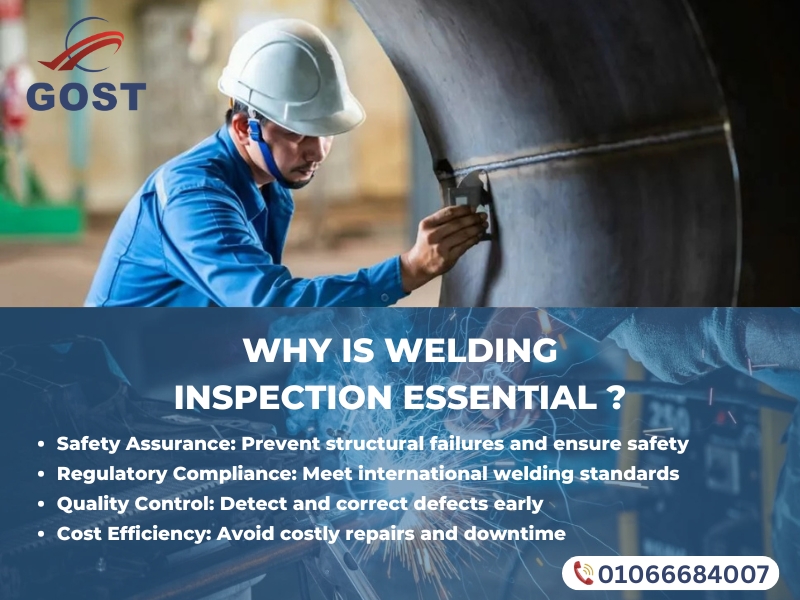
In industries where welded structures must meet strict safety and performance requirements, welding inspection services play a crucial role in maintaining quality and regulatory compliance. These inspections ensure that every weld adheres to international standards, preventing defects that could lead to operational failures. By identifying issues early, businesses can avoid costly repairs, minimize downtime, and enhance the longevity of their welded components.
Ensuring Compliance with International Standards
Welding is governed by strict regulations to guarantee the safety and reliability of structures in industries such as oil and gas, construction, and manufacturing. Welding inspection services help businesses comply with industry standards like AWS (American Welding Society), ASME (American Society of Mechanical Engineers), and ISO certifications, ensuring that welds meet required specifications. Compliance not only reduces the risk of structural failure but also protects companies from legal liabilities and financial penalties.
Detecting Defects Before Failures Occur
Undetected welding defects—such as cracks, porosity, and incomplete fusion—can weaken structures and cause severe failures. Through NDT welding inspection, experts use advanced techniques like ultrasonic weld inspection and radiographic testing to identify imperfections before they compromise performance. By detecting issues early, businesses can take corrective action, preventing costly breakdowns and safety hazards.
Reducing Downtime and Costly Repairs
Equipment failures due to poor welding quality can halt operations, leading to unplanned downtime and financial losses. Regular welding inspection and quality control help prevent unexpected shutdowns by ensuring that welds are strong and defect-free. By investing in professional Welding inspection services, industries can extend the lifespan of their equipment, reduce maintenance costs, and improve overall operational efficiency.
Methods Used in Welding Inspection Services
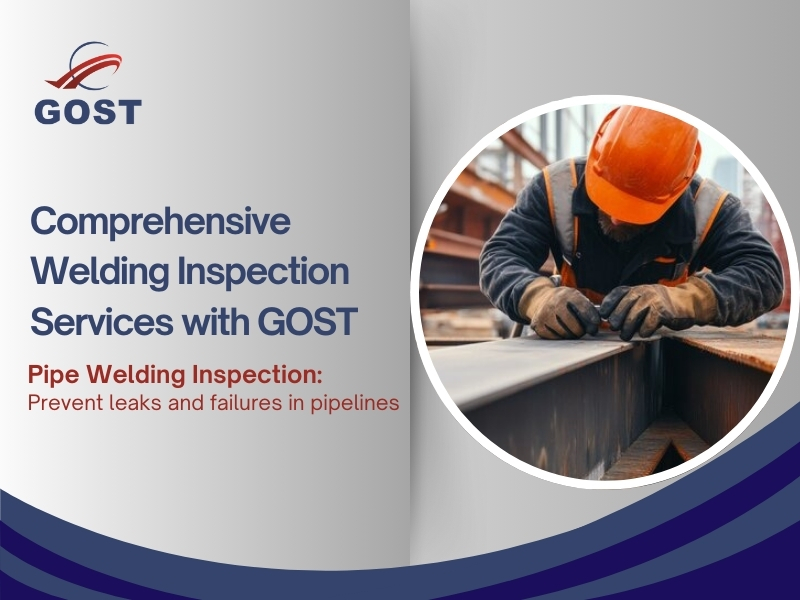
Welding inspection services rely on advanced techniques to ensure the strength, durability, and safety of welded structures. A single undetected defect can compromise an entire system, leading to costly failures. To prevent this, experts use a combination of visual assessments and non-destructive testing (NDT) methods to identify surface and internal flaws. Whether it’s ultrasonic weld inspection for detecting hidden cracks or pipe welding inspection gauges for precise measurements, each method plays a crucial role in ensuring weld integrity.
Visual Inspection – The First Step in Welding Quality Control
Before employing sophisticated testing methods, inspectors begin with visual weld inspection, a fundamental step in quality control. This method helps identify surface imperfections early, reducing the risk of defective welds being used in critical applications.
A trained inspector examines the weld bead, joint alignment, and overall quality using specialized tools. If irregularities like cracks, undercuts, or porosity are detected, corrective actions can be taken immediately, preventing costly failures down the line.
How Visual Inspection Identifies Surface Defects
Surface flaws are often the first sign of deeper welding issues. By closely analyzing the weld, inspectors can spot inconsistencies that may indicate improper fusion, overheating, or contamination. Catching these defects at an early stage ensures that necessary repairs are made before proceeding to more complex welding and inspection processes.
Tools and Techniques Used in Visual Weld Inspection
While visual inspections rely on the human eye, advanced tools like weld gauges, magnifiers, and digital imaging systems enhance accuracy. High-intensity lighting is used to illuminate weld surfaces, ensuring even the smallest irregularities are detected. In hard-to-reach areas, borescopes and remote cameras provide a detailed view, allowing inspectors to maintain high-quality standards.
Non-Destructive Testing (NDT) for Welding Inspection
Not all welding defects are visible to the naked eye. This is where NDT welding inspection techniques come into play, allowing experts to assess weld quality without causing any damage to the structure.
By using advanced testing methods, inspectors can detect internal flaws such as cracks, lack of fusion, or gas pockets that weaken the weld over time. These tests provide precise results without compromising the integrity of the material, making them an essential part of welding inspection and quality control.
Overview of NDT Techniques Used in Welding Inspections
Different NDT methods are used based on the material type, weld location, and required accuracy. Some of the most effective techniques include:
- Ultrasonic weld inspection – Uses high-frequency sound waves to detect internal flaws.
- Radiographic testing (RT) – Captures X-ray images of welds to identify internal discontinuities.
- Magnetic particle inspection (MPI) – Ideal for detecting surface cracks in ferromagnetic materials.
- Dye penetrant testing (PT) – Highlights surface defects by applying a special dye and developer.
Benefits of NDT Welding Inspection for Structural Assessment
NDT techniques offer unmatched accuracy and efficiency, making them the preferred choice for industries like oil and gas, construction, and power generation. These inspections ensure compliance with welding inspection companies’ safety standards while minimizing downtime. By identifying defects before they cause failures, businesses can maintain operational efficiency and avoid costly repairs.
Ultrasonic Weld Inspection – Detecting Internal Flaws
For applications where weld integrity is critical, ultrasonic weld inspection is one of the most reliable methods. This technique uses high-frequency sound waves to penetrate the material, detecting internal defects that might compromise structural safety.
How Ultrasonic Testing Ensures Weld Integrity
During an ultrasonic test, a transducer sends sound waves into the weld. If the waves encounter an irregularity, they reflect back, providing data on the defect’s size and location. This method is highly effective in identifying internal cracks, voids, and lack of fusion—issues that visual inspection alone cannot detect.
Advantages of Using Ultrasonic Inspection in Critical Applications
Industries dealing with high-pressure pipelines, bridges, and aircraft structures depend on ultrasonic weld inspection for its precision. Unlike radiographic testing, which requires radiation precautions, ultrasonic testing is safer, faster, and highly accurate, making it a preferred choice for non-destructive weld analysis.
Pipe Welding Inspection and Measurement Techniques
Pipelines must endure high pressure and environmental stresses, making pipe welding inspection essential for ensuring their durability. Faulty welds can lead to leaks, system failures, and hazardous accidents, emphasizing the need for rigorous inspection protocols.
The Importance of Pipe Welding Inspection Gauge
One of the most important tools for pipeline weld assessments is the pipe welding inspection gauge. This device measures key weld parameters, including thickness, reinforcement height, and misalignment. Accurate readings help inspectors verify compliance with industry standards, reducing the risk of structural weaknesses.
How Pipe Welding Inspection Prevents Leaks and Failures
A combination of visual, ultrasonic, and NDT welding inspection techniques is used to ensure that pipeline welds are free from defects. Detecting and correcting irregularities early prevents costly shutdowns and enhances the lifespan of the welded structure. By prioritizing thorough inspections, businesses can safeguard their operations and maintain industry compliance.
Key Factors in Welding Inspection and Quality Control
Welding inspection is more than just checking welds for visible defects; it involves precise measurements, thorough documentation, and strict adherence to industry standards. A small flaw in a weld can weaken an entire structure, leading to potential failures. That’s why welding inspection services focus on accuracy, compliance, and defect detection to guarantee long-term durability.
Importance of Precise Measurements and Documentation
Every weld must meet specific dimensional and structural requirements, which is why accurate measurements are crucial in welding and inspection. Inspectors use advanced tools such as calipers, micrometers, and pipe welding inspection gauges to assess weld thickness, alignment, and reinforcement height. These measurements help confirm that the weld meets international safety codes.
In addition to measurements, detailed documentation plays a vital role in welding inspection and quality control. Inspection reports record all findings, including test results, welding parameters, and any detected defects. This data is essential for audits, regulatory compliance, and ensuring that welding procedures are consistently followed in future projects.
How Welding Inspection Companies Ensure Compliance
Strict regulations govern welding standards, and welding inspection companies play a key role in ensuring compliance with industry codes such as:
- AWS (American Welding Society) – Standards for structural welding
- API (American Petroleum Institute) – Guidelines for oil and gas pipelines
- ASME (American Society of Mechanical Engineers) – Codes for pressure vessels and piping
To achieve compliance, inspectors assess weld quality using both visual and non-destructive testing (NDT) welding inspection methods. If any irregularities are found, corrective actions must be taken before the structure is approved for use. This rigorous process helps prevent failures and guarantees the reliability of welded components in industries like construction, power generation, and manufacturing.
Common Welding Defects and Their Impact on Structural Integrity
Even minor defects can weaken a weld, affecting the strength and performance of a structure. Some of the most common welding defects include:
- Cracks – Can lead to sudden structural failure under stress
- Porosity – Small gas pockets that reduce weld strength
- Lack of fusion – Insufficient bonding between the weld and base material
- Undercut – A groove at the weld toe that weakens the joint
How to Choose the Right Welding Inspection Company
Selecting the right welding inspection company is critical to ensuring the safety, durability, and compliance of your welded structures. Not all service providers offer the same level of expertise, so understanding what to look for can save you time, money, and potential risks.
Key Factors to Consider When Selecting a Service Provider
When choosing a company for welding inspection services, consider the following:
- Industry Expertise – Ensure the company has experience in your specific industry, whether it’s oil and gas, construction, manufacturing, or power generation.
- Testing Capabilities – A reliable provider should offer a full range of inspection methods, including ultrasonic weld inspection, visual inspection, and NDT welding inspection to detect all possible defects.
- Advanced Equipment – Modern inspection tools, such as pipe welding inspection gauges and ultrasonic testing devices, improve accuracy and efficiency.
- Reputation and Reviews – Check client testimonials, project history, and case studies to assess the company’s reliability and past performance.
Why Certification and Experience Matter in Welding and Inspection
A trusted welding inspection company must have certified inspectors with extensive field experience. Look for professionals accredited by recognized industry bodies such as:
- PCN (Personnel Certification in Non-Destructive Testing)
- AWS (American Welding Society)
- ASNT (American Society for Non-Destructive Testing)
- API (American Petroleum Institute)
Contact GOST Egypt for Professional Welding Inspection Services
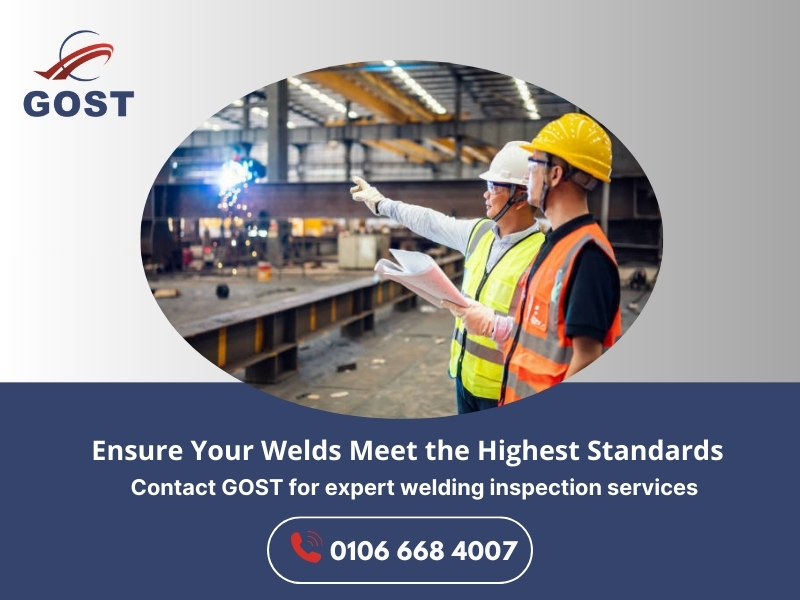
When precision, safety, and compliance matter, GOST Egypt is your trusted partner for welding inspection services. Our team of certified professionals brings extensive experience and state-of-the-art inspection techniques to ensure your welded structures meet international standards.
How to Get in Touch for Expert Consultation
GOST Egypt offers tailored inspection solutions to meet your project’s requirements. Whether you need NDT welding inspection, ultrasonic weld inspection, or pipe welding inspection, we are here to help. Contact us today to discuss your inspection needs and schedule a consultation with our experts.
Head office
- Address: 122 Galal El Desouki Street, Wabor Elmyah,
- Bab Sharki, Royal Palace tower ,Alexandria, Egypt
- Email: info@gostegypt.com
- Phone: +2 03 4228 204 – 4228 234
- Mobile: +2 0106 668 4007
- Fax: +2 03 4228 234
Cairo office
- Address: 8 El Sudan Street, El Dokki,
- Cairo, Egypt
- Email: cairo@gostegypt.com
- Phone: +2 02 3760 6450
- Mobile: +2 0109 002 6744
- Fax: +2 02 3760 6450
Ensure the integrity of your welded structures with expert welding inspection services from GOST Egypt. Get in touch today and let us help you maintain the highest level of quality and safety in your projects!
FAQs
What Is Welding Inspection?
Welding inspection is the process of evaluating welded joints to ensure they meet quality, safety, and compliance standards. It involves examining welds for defects, inconsistencies, and structural integrity issues that could lead to failures. A proper welding inspection service ensures that welds comply with international standards, industry regulations, and project requirements.
How Do You Inspect Welding Quality?
Inspecting welding quality involves a combination of visual inspection, non-destructive testing (NDT), and destructive testing methods:
- Visual Inspection (VT)
- Ultrasonic Weld Inspection (UT)
- Radiographic Testing (RT)
- Magnetic Particle Testing (MT)
- Liquid Penetrant Testing (PT)
Each method ensures that welds meet welding inspection and quality control standards, preventing failures and costly repairs.
What Is an NDT Welding Inspector?
An NDT welding inspector is a certified professional specializing in non-destructive testing (NDT) for welding inspection. Their role is to evaluate weld integrity without causing damage, ensuring compliance with international codes like AWS, ASME, and ISO standards.
These inspectors use advanced testing techniques such as ultrasonic weld inspection, radiographic testing, and pipe welding inspection gauges to identify defects before they lead to structural issues. Certification from organizations like ASNT, PCN, AWS, or API guarantees their expertise in detecting welding flaws and ensuring quality.
How to Test If a Weld Is Good?
A good weld must be strong, defect-free, and meet industry standards. Testing methods include:
- Visual Inspection
- Non-Destructive Testing (NDT)
- Mechanical Testing
- Pipe Welding Inspection Gauge
By applying these testing methods, welding inspection companies guarantee weld quality, structural integrity, and long-term reliability.